5 Tips for moving pallets in a warehouse
Pallets often get damaged due to poor handling in the warehouse. The vast majority of pallet rack structural failure stems from 3 main sources:
- Impacts from collisions with pallet and lift trucks
- Misuse of racks and overloading
- General lack of a safety-oriented mindset
Much of this damage occurs when pallets are being moved in the warehouse. Here are 5 tips that will help you keep your pallets safe when moving them inside the warehouse.
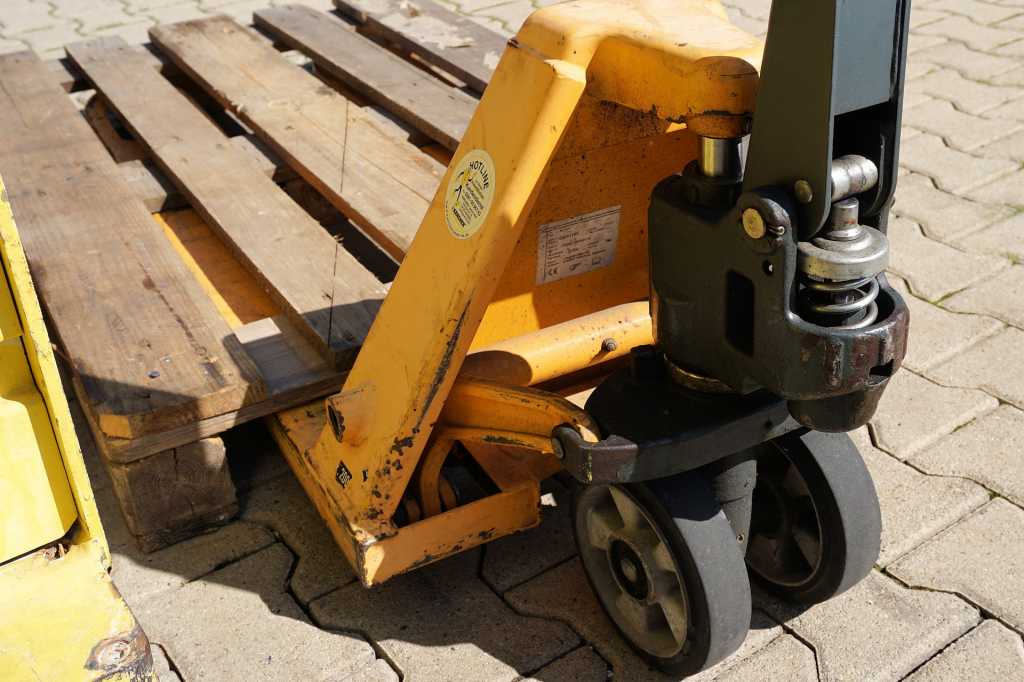
5 Tips for moving pallets
1. Place the Load Squarely
Pallet truck drivers should be trained on how to deposit pallets correctly on rack beams. The pallets should be placed squarely, and should overlap uniformly on the front and the back whenever possible. This helps to maintain evenly-distributed loads in order to maximise rack capacity and save wear on the beams. Pallets that are out of square can easily cause accidents when they are stacked in two or more rows. On the other hand, placing the load onto wire decks leaves the pallet unsupported by rack beams and can greatly reduce capacity.
2. Proper Training of Pallet Truck Drivers
Pallet truck drivers should be properly trained to always observe the following steps when moving pallets in the warehouse:
- Always face directly in the direction you are going
- Carefully assess the space in front of the truck for potential hazards keeping in mind that pallet truck wheels are small and can get easily jammed in narrow spaces
- Always secure your load before moving it
- Walk slowly when pushing the pallet truck
- Never exceed the stated maximum capacity of the cart
- Go in reverse when going down an incline to avoid losing control of the truck
- Use gloves when pushing the truck to avoid injury
- Avoid making sharp turns and slow down when turning corners
- Avoid leaving the truck sitting on an incline
- Take your forklift and pallet truck drivers for refresher courses about once a year
3. Use Guardrails
The ends and corners of rack aisles tend to be highly susceptible to direct hits by pallet trucks. Use steel guard rails and post protectors that are placed 1’ to 3’ in front of the deck to protect your pallets. Make sure you guard your rack bays using wire guards or netting. These are relatively inexpensive yet highly invaluable in areas where there is order picking and lots of foot traffic.
4. Never Exceed the Listed Capacity
This might sound fairly obvious yet many warehouses find it difficult to enforce it. It really boils down to proper documentation, training and optimal product distribution. Train your warehouse men to understand the capacity of your racks and the average weights of different loads. Post the capacities on the racks so that the drivers can see at a glance how much the beams can handle.
Beam capacity is easier to understand for many people than upright capacity. The rule of thumb is that the greater the vertical space between consecutive beam shelves, the lower the upright capacity.
5. Regular Maintenance
Rack accidents are frequently caused by improper installation. Boltless beams should be secured to the rack. The rivets should fit snugly and safety clips utilised. Replace damaged racks.
Some areas have high seismic activity and require the racks to be modified. Understand your local, federal or state seismic regulations and stick to them. By observing these simple yet useful tips, you can avoid many of the warehouse accidents and minimise damage to your pallets.
For premier forklift training, including for hand truck pallet drivers, simply contact us here at Euro 1 Training and we’ll be happy to help.